Test & ATE Power Distribution Units
National Instruments
Custom ATE Racks
When N.I. developed the program to create its turn-key ATE Core solutions for their customers, they turned to Marway to provide the power distribution. Standardized models were developed to cover a range of applications.
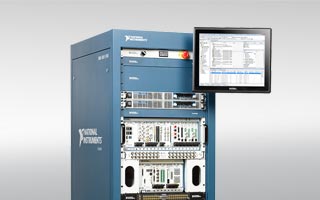
KLA
Semiconductor ATE
KLA designs and manufactures multiple tools for semiconductor manufacturing including test and metrology. Marway designed and manufactured a power distribution module for the line of KLA SpectraFx models.
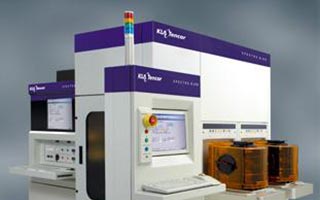
NGATS
Field Test & Support
This unit distributes and monitors power in multiple power forms for a variety of application and computing equipment. Designed and tested to various sections of 810, 167, 1399, and MIL-HDBK-217 standards.

Meeting the Needs of Test Power
Test applications, and the testing equipment used, vary as much as the products being tested — as does the power distribution needed to power the test setup. Some have common requirements with just that one special twist which can be impossible to find. Others have highly specialized needs in power conditioning, multiple power forms, switching interlocks, and connectors which requires engineering and manufacturing experience to develop.
Marway has been meeting the specialized needs of test and automated test power distribution for decades. We’ve done countless slightly modified variations of existing designs to meet those “just the same as, except...” cases that other companies won’t do. And we specialize in doing those top-to-bottom custom designs that very few companies even could do.
We can create test PDUs from cost-effective commercial solutions, engineering-demanding R&D systems, to deployed military depot diagnostic platforms. Not only has Marway gained the experience to meet the technical requirements of our customers, we’ve also developed the partnership services to support the different types of customers we serve.
What to look for in a test station PDU ↑
- Protects downstream equipment from noisy facility power using EMI filters, surge suppressors, and other techniques.
- Saves space by integrating conditioning and conversion needs instead of housing them as external boxes.
- Improves integration by providing the exact connectivity and controls needed for site-specific equipment.
- Complies with general and industry-specific standards for electrical power handling equipment.
What to look for in a PDU supplier ↑
- Takes the time to understand the application, explore needs, and consider design options.
- Optimizes the selection of application-specific components for capacity matching, packaging efficiency, and cost.
- Designs and manufactures enclosures to meet unique needs for installation, cable routing, and other integration details.
- Manages the entire process of standards testing and certification, when required, prior to delivery.
Serving OEMs, VARs, and End Users ↑
- Single unit and low volume customization is our speciality.
- Capacity to deliver higher volumes of hundreds to thousands of units a year.
- PDU family design management to minimize OEM SKUs.
- Logistics partnership to help manage OEM production.
Your choice of custom or standard ↑
- Marway specializes in application-specific PDUs.
- Rackmount chassis from 0U to 24U, to rack sized.
- Custom enclosures for non-rack applications.
- Ac, dc, up to 600 volts, 400 amps.
- We also have nearly 300 standard basic and smart PDUs.
- 1-phase, 3-phase, 15-, 20-, and 30-amp models.
- 1U, 2U, 3U, and vertical 0U configurations.
Integrated conditioning, conversion, and control ↑
- Reduce EMI using filters and other techniques.
- Mitigate voltage spikes/transients using surge suppression.
- Integrate ac and dc sources into a single system.
- Use integrated conversions to create needed power forms.
- Optimize local and remote power monitoring and switching.
- Improve safety with EPO and interlock circuit integration.
Networked or non-networked controls ↑
- Non-networked PDUs still offer some remote switching through discrete signals from remote panels.
- Networked PDUs offer remote outlet switching and power monitoring over HTTP/S, SSH, Telnet, and SNMP.
- Automated outlet control and periodic data collection is scriptable through Telnet, SSH, SNMP, or RESTful API.
Standards and compliance management ↑
- Certified ISO 9001 (with AS9100).
- Products designed and manufactured to UL/IEC 62368-1 and 61010-1 (others when required).
- UL and CE certification (others when required).
- MIL-STDs in support of development for land, air, and shipboard applications.


Cleaning Up Noisy Power ↑
Noisy facility power signals occur in factories, test labs, service depots, and other environments due to the varying loads of nearby high-powered equipment like motors, switching power supplies, even office A/C and lighting. Whether the noise comes from the next bench over, or the lab down the hall, or just building infrastructure, it can adversely affect test equipment.
Like sudden water pressure surges cause pipes to rattle, sudden surges of “pressure” and “flow” (voltage and current) in electrical lines cause signal abnormalities. Where a weak fitting along a pipe might leak, a vulnerable component in an electronic system may fail.
Most commodity PDUs are designed for office-like environments where there is little impact from power signals on office equipment. At most, these PDUs may have some surge protection since those devices are relatively low cost and small.
For point-of-use bench testing or OEM automated test equipment where clean power is essential, a PDU designed for test applications integrates surge suppression, EMI filters, isolation transformers, and other tools to mitigate noise. Selecting these components requires an understanding of the types of noise which are expected in the environment, and matching various attributes of the components to the power form being conditioned.
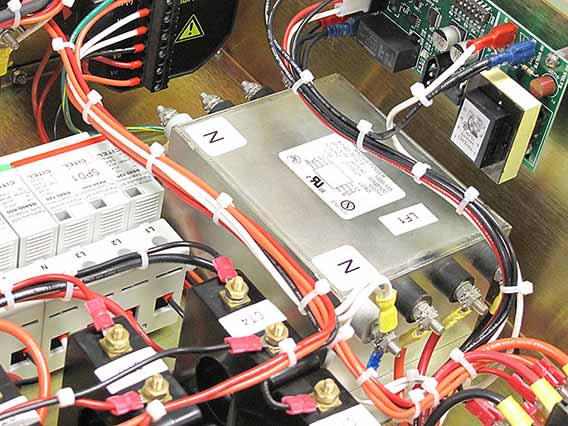
Creating Needed Power Forms ↑
Many test environments need a mixture of different power forms. A power form is the combination of specifications for voltage type, voltage rating, and current rating. For example, 120 Vac, 15 amps vs. 80 Vdc 60 amps are two different power forms.
A building’s facility power will usually be wired for two or three forms, but they won’t all be routed to all work areas. In industrial or commercial buildings, this is most typically three-phase ac power for some areas in addition to common 120 volt wall outlets. In various manufacturing or laboratory stations, there may be a need for more types of power. Ac may be needed in multiple three-phase and single-phase forms. Different voltages may be needed to serve the larger and smaller pieces of equipment. Even dc power is often needed in the same work spaces.
Test PDUs can integrate transformers, power supplies, and power converters to create multiple power forms from a single facility wall source. This can simplify installation, and save space and cost.

Meeting Exact Control and Connection Needs ↑
Test and ATE PDUs offer a wider range of circuit designs, control features, power monitoring, and even remote management capabilities. Most commodity power distribution products have a single circuit serving all outlets with perhaps an on/off switch or breaker. Test environments often require more control over multiple individual circuits. Digital displays to power quality meters assure that power is being delivered as required. Indicators for the status of specific circuits and interlocks are simple additions, but unique to each application. Adapting to these unique switching, display, and control needs, is key to a productive PDU in a test environment.
Another area of important flexibility is that of cable connectors. Between test equipment and the device under test, there are hundreds of unique connectors to contend with. There are standardized ac power connectors, but even then there are dozens of types depending on voltage, current, safety features like locking, resistance to water, vibration, and more. Control signal connectors are even more varied. Integration to external interlocks, sensors, and more require that a PDU have the flexibility to incorporate what an application needs.
